- Rédigé par : Vincent
- Mis en ligne le :
- Temps de lecture : 5 min
Remettre en cause son modèle pour améliorer sa performance industrielle nécessite quelques phases de travail en amont de la démarche. La réflexion peut s’organiser autour de quelques étapes simples en apparence, mais qui nécessitent une prise de recul et une objectivité les plus importantes possibles. Chaque étape de la transformation peut également être accompagnée par des professionnels, un cabinet conseil en performance industrielle par exemple, pour gagner en objectivité.
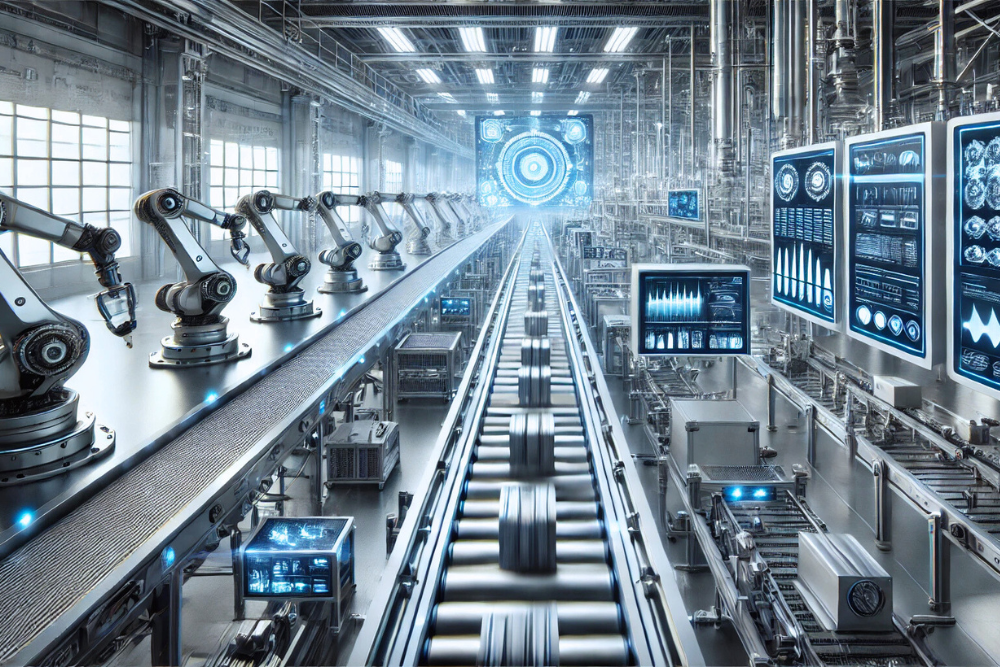
Table des matières
Voici 5 étapes-clés pour amorcer un nouveau processus d’amélioration de la performance industrielle :
Etape 1 : Analyser les indicateurs existants
Il s’agit tout d’abord d’analyser les indicateurs existants pour vérifier leur adéquation avec les nouveaux objectifs de la performance. Classiquement, les indicateurs portent sur les coûts, les délais, la qualité, les livraisons, etc. C’est la partie émergée de l’iceberg. Les indicateurs intermédiaires évoluent pour s’adapter aux nouveaux schémas et surtout à la demande d’instantanéité de consommation des produits. Ces indicateurs peuvent être partagés, connectés avec les fournisseurs, les distributeurs et/ou les utilisateurs finaux pour gagner en efficacité et en transparence.
Prenons l’exemple d’un industriel en horlogerie. Pour répondre aux demandes croissantes et immédiates de ses clients, il a mis en place un système d’information et d’indicateurs avec ses sous-traitants. Ce système lui permet de voir en temps réel le niveau de charge de leurs usines pour sélectionner le plus capacitaire sur une commande donnée.
Pour aller plus loin, consultez notre article « Optimiser le planning de production avec Delmia ORTEMS de Dassault Systèmes«
Etape 2 : Changer l’angle de vue et les méthodes de travail
Des process peuvent apparaître comme optimisés pour les équipes alors qu’avec un nouvel angle de vue, ils pourraient gagner en efficacité. Le test de différentes configurations au fur et à mesure des années, l’expérience de ce qui fonctionne, peut amener les opérateurs les plus chevronnés à verrouiller les solutions possibles. De même, une tâche exécutée de manière répétitive empêche souvent les collaborateurs de prendre du recul par rapport à l’organisation globale du travail. Le process global des opérations doit être intégralement revu pour améliorer la performance industrielle. Pour cela, du recul et souvent un changement d’angle de vue sont nécessaires.
Prenons cette fois-ci l’exemple d’un fabricant de fibre optique et de connecteurs. Ce fabricant employait 4 opérateurs pour le rangement des stocks et 4 autres opérateurs pour renseigner les clients sur les plannings de livraison. En mettant en place un système de gestion automatisée des stocks et de tracking sur internet, les clients ont pu avoir une information en temps réel des plannings de livraison, tout en améliorant le visu sur les stocks de composants. Les opérateurs ont pu voir leurs missions évoluer vers du pilotage de stock, des rotations, et de la supervision des plannings et des livraisons.
Etape 3 : S’autoriser des méthodes innovantes
Lorsque le dirigeant ou l’équipe de production imagine un nouveau système, ils doit s’autoriser à imaginer les méthodes les plus innovantes dans le domaine. Le digital offre de nombreuses possibilités, dont certaines encore non exploitées à ce jour. Il faut sortir des idées de faisabilité pré-conçues, avoir un esprit disruptif, pour imaginer un schéma idéal dont la faisabilité peut être réelle grâce aux champs des possibilités offertes par le numérique.
Etape 4 : Benchmarker les technologies émergentes
- Et si l’ensemble des technologies que nous utilisons au quotidien dans notre vie privée pouvait être transposé à l’industrie?
- Pourquoi ne pourrait-on pas tracker ses livraisons industrielles comme nos colis depuis un site e-commerce ?
- Personnaliser à l’envie et recevoir son produit, peu importe lequel, son volume ou ses quantités, en 24h?
L’important dans ce processus de réflexion est de chercher et repérer ce qui pourrait bénéficier à son modèle industriel et être adapté à son appareil productif. Certains services et technologies que nous utilisons au quotidien pour la plupart, personnels ou professionnels, profitent de nombreuses innovations qui pourraient s’adapter à l’industrie pour améliorer la performance globale et le service rendu au client.
S’intéresser à tout, ouvrir la curiosité à des champs radicalement différents des références actuelles, telle est la mission des industriels aujourd’hui pour innover dans leurs process industriels. Et pour ce faire, industriels et clients peuvent étudier ensemble les solutions possibles.
Etape 5 : Travailler en partenariat avec ses clients
« On innove qu’à plusieurs »
Travailler en partenariat avec ses clients permet d’être au plus près des besoins et surtout des réponses que l’on peut apporter à son client. L’objectif commun étant la performance, l’intérêt réside dans la construction commune de l’offre, tout en prenant en compte les contraintes et les possibilités de chacun.
Il s’agit de travailler avec une approche type Design Thinking avec son client pour améliorer la créativité, la recherche de solutions et accroître l’agilité de part et d’autre. L’idéal est de pouvoir créer le projet ensemble en y allant par étapes, mettre en application des changements restreints pour tester et évaluer les enjeux au fur et à mesure de l’avancement.
Pour y parvenir, il ne s’agit pas d’établir un cahier des charges précis, mais de créer un prototype ensemble, puis de l’adapter ensemble via des outils collaboratifs. Le partage de l’information est essentiel pour prototyper efficacement des solutions. De cette manière, la performance est atteinte plus rapidement puisque la solution la plus juste est elle-même trouvée plus rapidement.
Grâce à cette méthode, le gain de temps sur les projets peut atteindre 15% par rapport à des process plus classiques basés sur des cahiers des charges. La technologie facilite ce mode collaboratif.
Conclusion, la performance industrielle nécessite une remise en cause de nombreux schémas établis.
L’idéal est de pouvoir s’appuyer sur des cabinets-conseil pour bénéficier d’un œil extérieur, objectif, et d’un accompagnement au changement.Le travail collaboratif avec un cabinet mais surtout en aval avec les clients permet d’enrichir l’éventail des possibilités, de répondre au plus près des besoins du client, et de gagner du temps sur l’ensemble du projet. Vous avez un projet ? Demandez à être rappelé gratuitement par un de nos consultants en performance industrielle : Contactez-nous !